FFM - Flash Floc Mixing Systems
Applied Mechanical Technology is an industry leader in industrial wastewater treatment components and systems. Since 1997 we’ve been designing and building industrial equipment and systems for variety of industries.
We design and build all our core technology equipment in-house. Our complete line of equipment includes:
- Oil Water Separators,
- DAF Dissolved Air Flotation,
- Inclined plate Clarifiers,
- Multimedia filters
- Controls Packages.
These are the core of our complete systems packages. We complete our systems with strategic OEM relationships for all the other necessary components such as instruments, pumps, valves etc.
As we design and manufacture our core equipment and systems in our own shop we have the flexibility and the ability to configure our systems as needed to meet the most stringent project specifications while exceeding customer’s expectations.
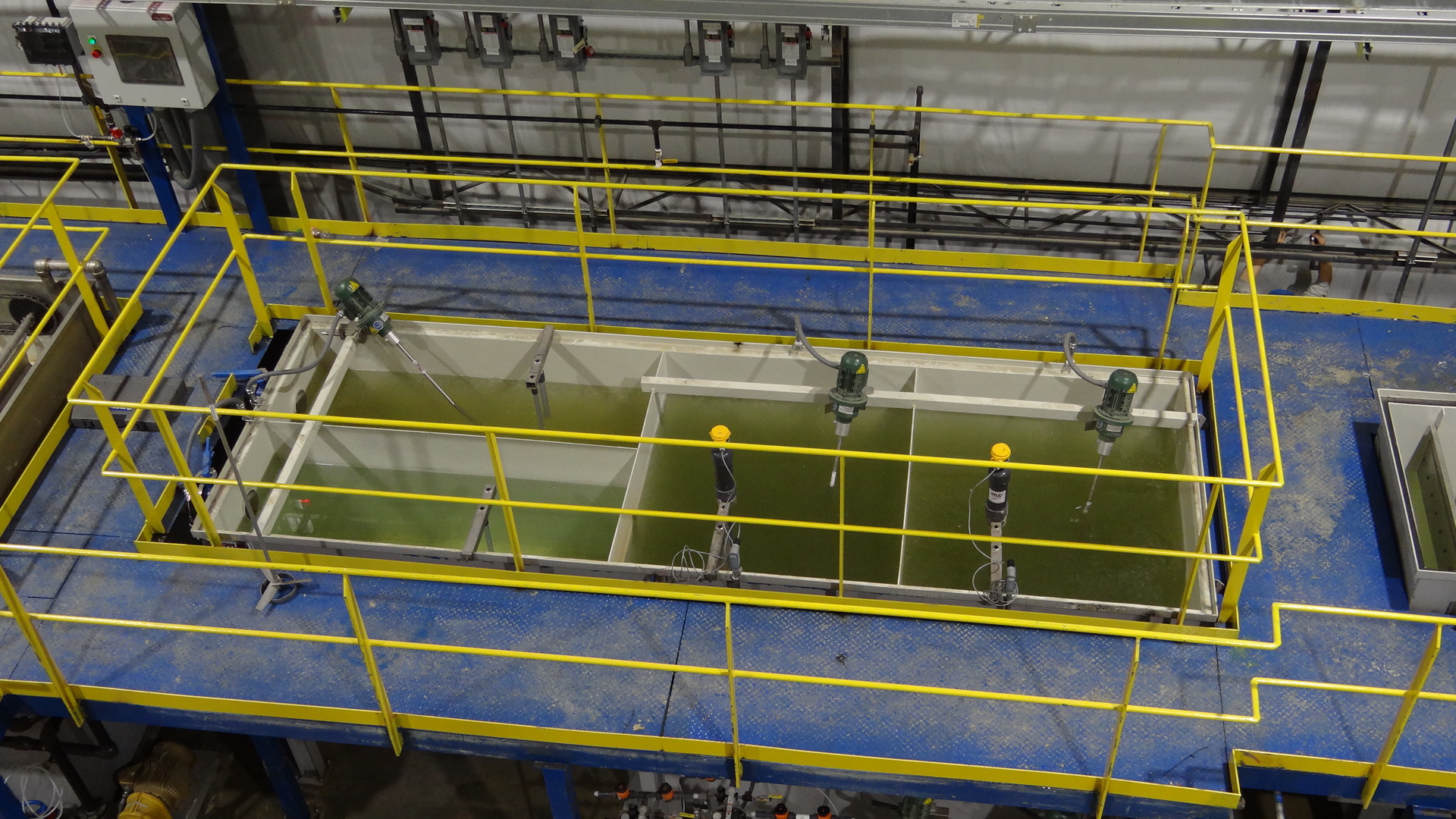
Principal of Operation – FFM Flash Floc Mixing Systems
FFM Flash Floc Mixing Systems are systems that precede Clarifiers and DAF systems. They are the chemical enhancement system that makes good treatment results possible. Without them we could not break emulsions, precipitate metals or agglomerate solids. They are the workhorse before the separator (DAF and Clarifiers are technically separators). If the FFM or its chemistry are not working properly neither will the DAF or Clarifier – period.
The ultimate purpose of the FFM is to create particles of sufficient mass that can rapidly settle in a clarifier or of a mass capable of entraining bubbles (from a DAF) in order to float easily. The choice of DAF or Clarifier is usually determined by treatability testing and observation. If the resulting floc tends to sink, then use a clarifier. If the resulting floc tends to float or is buoyant neutral then flotation in a DAF is indicated. Some applications are well known and therefore treatability testing is not necessary. An example of this is highly oily wastewater where we expect the floc to float due partially to the natural tendency of oil to want to float. Another example is a metal plating application where all metals and solids are targeted. This wastewater will definitely sink indicating a clarifier is appropriate.
FFM chamber residence times are very important to ensure reaction completion prior to the next chamber. Not all chambers are the same. Residence times are dictated by the task. For example, pH adjustment chambers are typically 10-15 minutes long, chromium residence times are typicall 20-40 minutes, oil emulsification residence times are typically 10-15 minutes, floc mixing times are typically 2-5 minutes residence. All chambers except floc mix are best served with rapid mixing (the Flash in FFM) while the floc mixing chamber is done with a variable speed mixer and a low shear type impellor.
There are many configurations of FFM system that is dictated by what the desired results are. Applied Mechanical Technology makes all our FFM systems to many standard designs as well as custom configurations to meet project specifics.
- Three Stage FFM. Typically used for emulsion breaking or chromium Cr+6 reduction.
First Stage. For emulsion breaking the 1st stage is typically acidification to break the emulsion bonds. For Cr reduction the first stage is typically for Cr+6 reduction to Cr+3 as Cr+6 is highly soluble. The reduction is accomplished with acidification in combination with an oxidizer such as sodium metabisulfite (Na2S2O5) to reach an ORP (Oxidative Reduction Potential) endpoint.
Second stage is where we create “pin floc”. It is the stage where reaction first becomes visible to the naked eye by forming tine pin head sized particle of precipitate. It’s first step is usually for pH elevation to precipitate solids, metals, demulsify oils, and to coagulate solids. Most coagulants, organic and inorganic tend to work better at elevated pH ~8. Coagulants typically fall into three categories, Iron Fe based typically used for metals applications, Aluminum or Alum (Al2SO4) based for oily based applications and high performance blends of various types, too many to mention here.
If metals are the goal they must be precipitated first using sodium hydroxide at an elevated pH. Different metals prefer different pH, see metal OH solubility chart here.Third Stage is for floc development. Floc is a special long chain polymer of either anionic or cationic charge that is used to agglomerate the “pin floc” created in the preceding stage. The pin floc will contain precipitated metals and/or demulsified oils and solids. Pin floc can be somewhat fragile and is best mixed with a variable speed mixer with operator control. If the floc is seen to break apart then the mixer is slowed to maintain mixing but not break the floc apart. Floc is important as it completes the process of creating sufficient mass to either be settled in a clarifier or floated in a DAF. As Applied Mechanical Technology makes both DAF and Clarifier we have no bias on the process.
- Two Stage FFM. Typically used for metals that do not need reduction (such as Cr+6), and ordinary solids.
First stage is where we create “pin floc”. It is the stage where reaction first becomes visible to the naked eye by forming tine pin head sized particle of precipitate. It’s first step is usually for pH elevation to precipitate and coagulate solids. Most coagulants, organic and inorganic tend to work better at elevated pH ~8. Coagulants typically fall into three categories, Iron Fe based typically used for metals applications, Aluminum or Alum (Al2SO4) based for oily based applications and high performance blends of various types, too many to mention here.
If metals are the goal they must be precipitated first using sodium hydroxide at an elevated pH. Different metals prefer different pH, see metal OH solubility chart here.Second Stage is for floc development. Floc is a special long chain polymer of either anionic or cationic charge that is used to agglomerate the “pin floc” created in the preceding stage. The pin floc will contain precipitated metals and/or solids. Pin floc can be somewhat fragile and is best mixed with a variable speed mixer with operator control. If the floc is seen to break apart then the mixer is slowed to maintain mixing but not break the floc apart. Floc is important as it completes the process of creating sufficient mass to either be settled in a clarifier or floated in a DAF. As Applied Mechanical Technology makes both DAF and Clarifier we have no bias on the process.
- Single Stage FFM is for floc development only. This is typically done in special applications where clarifying minimal solids is needed such as river water turbidity reduction where coagulants may not be needed. Floc is a special long chain polymer of either anionic or cationic charge that is used to agglomerate the “pin floc” created in the preceding stage. The pin floc will contain the agglomerated solids. Pin floc can be somewhat fragile and is best mixed with a variable speed mixer with operator control. If the floc is seen to break apart then the mixer is slowed to maintain mixing but not break the floc apart. Floc is important as it completes the process of creating sufficient mass to either be settled in a clarifier or floated in a DAF. As Applied Mechanical Technology makes both DAF and Clarifier we have no bias on the process.
Our FFM Systems are found in a variety of industries including but not limited to:
- Oily wastewater emulsification and coagulation
- Metal Forging press pit oily wastewater
- Metal plating and conversion coating
- Food processing.
- Groundwater remediation
- Solids removal
- Turbidity reduction
- Chemical Etch bath rinse waters
- Bottom fly ash sluice water
- Scrubber water
- Cooling tower water
Typical Options Include:
- Mild steel or stainless steel construction
- XP Explosion proof electrical components
- Bottom sludge augers
- Complete control packages
- Pump skids, inlet, effluent, sludge
- Chemical dosing and FFM Flash-Floc-Mixing Systems for emulsion breaking
- Operator platforms
- Special coatings for highly corrosive application
- Effluent filters
Need a Quote?
Click here for our Application Questionnaire to obtain a quote.
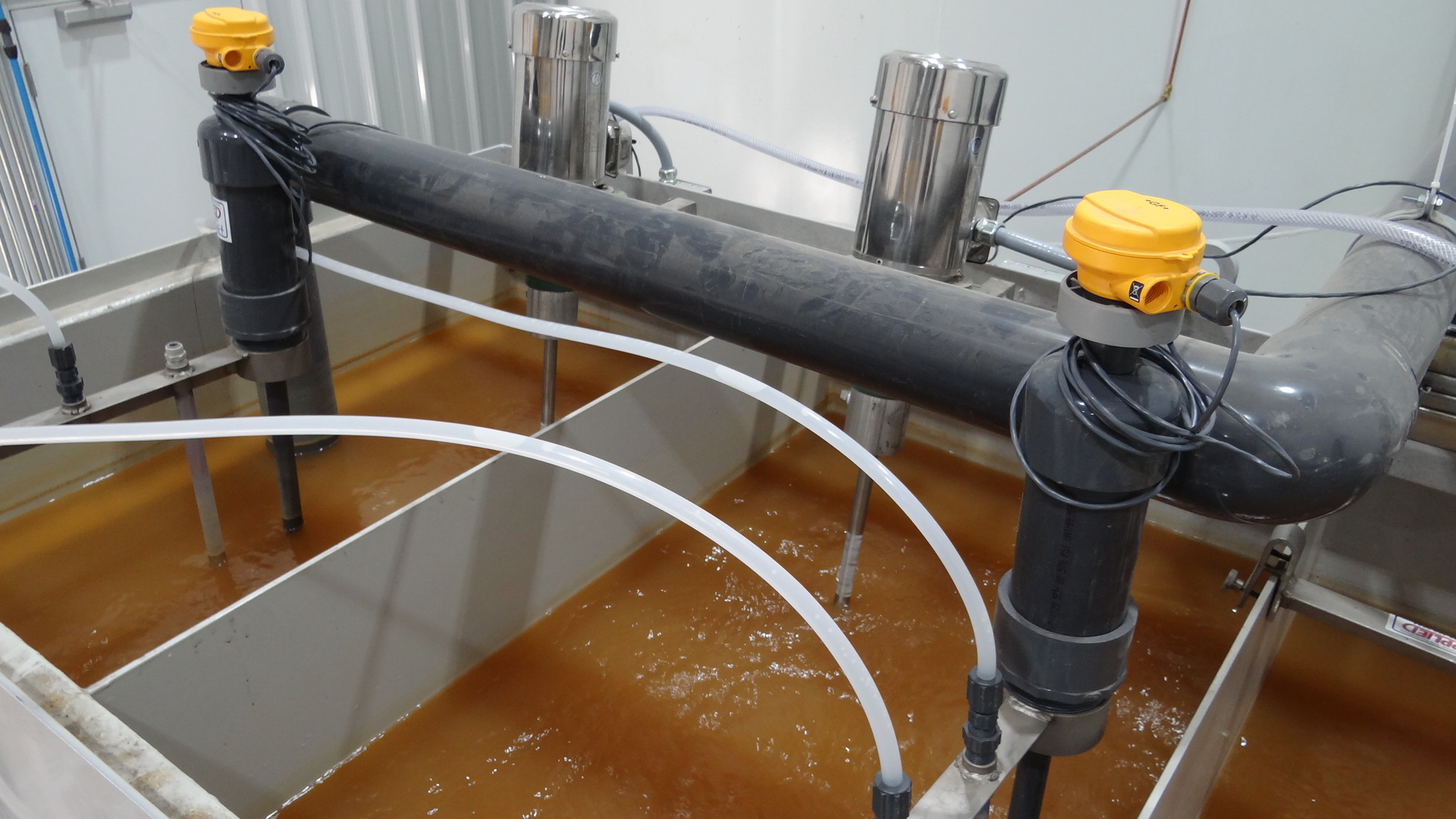
Quality
We use only the highest quality materials, pumps, instruments, valves and controls components to ensure you the heavy duty robust performance you demand in today’s highly competitive market environment. All our systems are built to the highest standards of craftsmanship and are extensively tested throughout the fabrication process. We perform a variety of NDE testing including PQR, UT, XT, full hydro, dye penetrant, ASME pressure testing and of course visual inspections and functional testing both in-shop and in the field.
Controls
Our operator controls interface scheme is the most advanced in the wastewater industry. We offer basic simplified controls to full featured controls systems that use SQL database platforms permitting the generation, archiving and managed all trending and effluent data. Our most advanced controls offer operator input of bench treatability testing that then allow the system.We design and build all our own controls in-house to UL-508A Industrial Control Panel standards with strict conformance to NEC ANSI/NFPA 70 regulations. All panels are built to UL standards and are individually UL certified if required.
Tankwash Systems
Our Industrial Tankwash Division designs and builds Railcar and Tank Trailer Internal wash systems to wash everything from Crude oil to Edible oils, from Chemicals to Corn Starch and everything in between. When you wash an industrial tank, you create an industrial wastewater and we take care of that too.