MMF MultiMedia Filters
Applied Mechanical Technology is an industry leader in industrial wastewater treatment components and systems. Since 1997 we’ve been designing and building industrial equipment and systems for variety of industries.
We design and build all our core technology equipment in-house. Our complete line of equipment includes:
- Oil Water Separators,
- DAF Dissolved Air Flotation,
- Inclined plate Clarifiers,
- Multimedia filters
- Controls Packages.
These are the core of our complete systems packages. We complete our systems with strategic OEM relationships for all the other necessary components such as instruments, pumps, valves etc.
As we design and manufacture our core equipment and systems in our own shop we have the flexibility and the ability to configure our systems as needed to meet the most stringent project specifications while exceeding customer’s expectations.
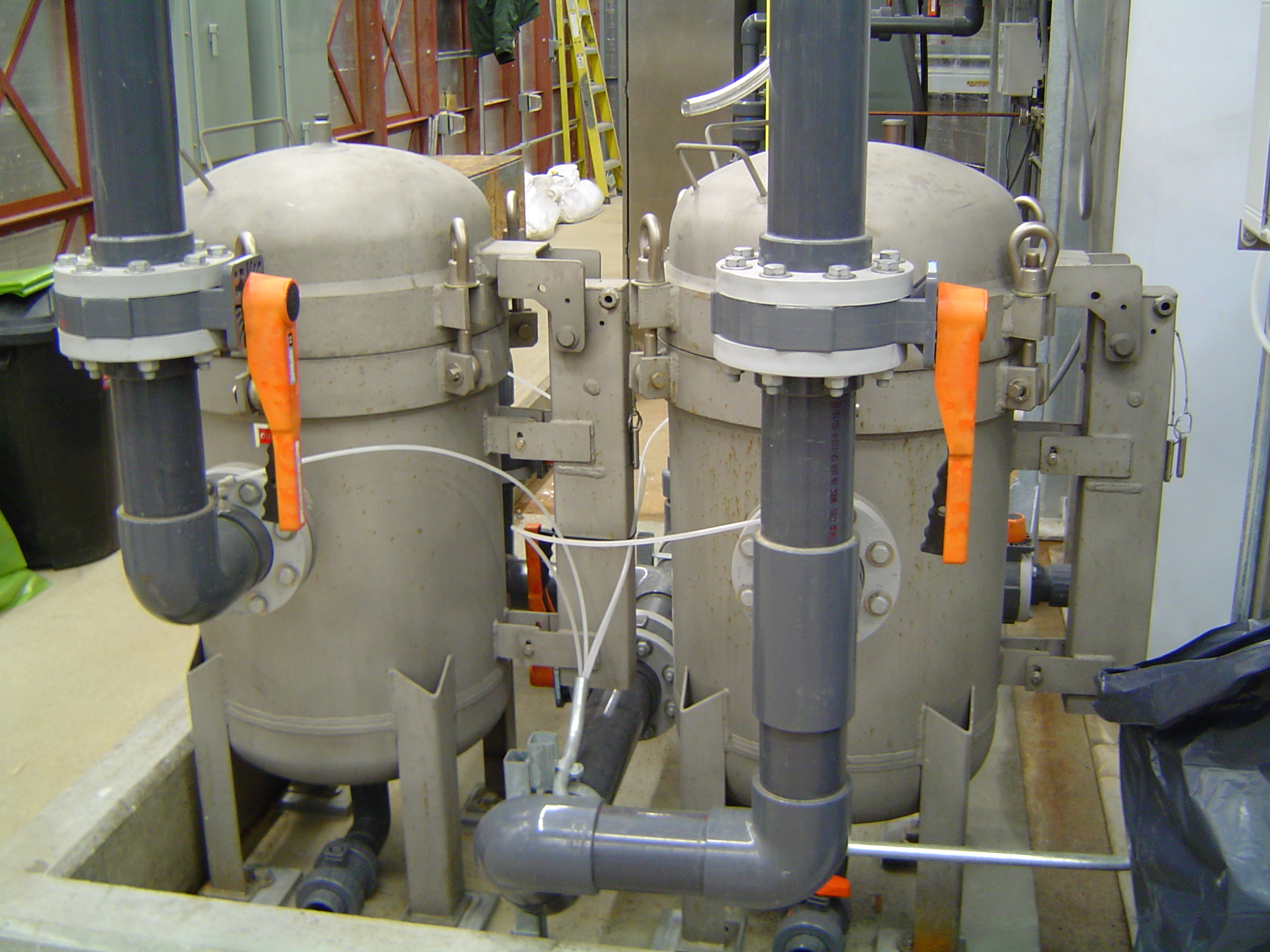
Principal of Operation – MultiMedia Filters
MultiMedia filters are essentially particle separators. That is to say that any particle larger than the collective effect of the media particles will be separated from the water. Generally speaking, a properly designed MMF can remove 10 to 15 micron particles. Visible particles are ~40 microns.
MMF Filters are typically used as polishing filters after DAF and Clarifier systems. A safety net if you will. They are also used for front end treatment of drinking water or for treating river and lake water that may be used for process, fire fighting, washdown, domestic sanitary flush water.
Filter Design. MMF filters have several standard configurations including, but not limited to;
- Single cell. When in backwash the process flow must stop.
- Dual cell. When one cell is in backwash the other is in service mode.
- Triple cell. When backwash is needed, one cell is in backwash and the other 2 cells provide the clean backwash water.
The filters work in a downward flow path gathering the filtered solids in the first few inches of the media surface. The inlet has a spoke tube type flow distributor that distributes flow evenly across the top of the media bed. The bottom has a slotted spoke distributor that directs effluent evenly across the outlet distributors and therefore evenly thru the bed. Typical filter Hydraulic Loading Ratios or HLR is 5 to 9 gpm/ft2 for industrial applications and 2 to 5 gpm for drinking water applications. Filters in general should be fed with no more than 50 ppm TSS Total Suspended Solids. More TSS will load the filter quickly causing excessive backwashing.
Backwashing filters. Automatic backwashing is the best configuration as it cleans itself as needed and keeps the process running. As the solids build up on the media bed the flow is decreased and a differential of pressure develops between inlet and outlet. This differential is measure by a sensor. When differential reaches between 10 to 15 PSID the filter needs to be backwashed. Backwashing is done by reversing flow from downward to upward. The same distributor manifolds are used but the flow rate is typically 15-20 gpm/ft2 of surface area or about 2-3 times the service flow rate. The backwash must be capable of fluidizing the media bed and the vessel must have 40-50% of total height as freeboard to permit the bed to fluidize without washing out media. Backwashing typically lasts 5 to 15 minutes.
Clean backwash water is needed to properly clean a filter. Typically the BW rate and quantity is such that tap water won’t be sufficient. A clean backwash water holding tank is needed. This tank can be on the outlet side of the filter receiving treated water and be maintained full so that when a backwash is needed it can supply the clean backwash water. Of course, the dirty backwash water has to be accommodated too.
Backwashing can be enhanced by adding optional features. If your filter will be subject to mineral deposits, hard water or sticky solids there is hope. One optional feature is to use air scouring where compressed air is added to the first few minutes of a backwash to really stir, tumble and fluidize the bed. For really severe service applications the MMF can be configured to drain the vessel to half empty, then the air scour is done without flow. Finally the backwash continues to wash out the solids. Another optional backwash feature is to use acid during a backwash. Very effective at dissolving mineral deposits but comes with some drawbacks such as handling the acid and neutralizing it afterward.
Media for MultiMedia filters are filters that typically contain gravel, garnet, sand, and sometimes anthracite. Not your garden variety rocks and sand, these are highly classified medias that conform to AWWA American Water Works Association B100 specifications and sieve analysis for uniformity of shape and size. When you hold a handful of garden sand you have every size particle possible in one handful, from dust to pebbles. When you hold AWWA B100 conforming sand filter media it’s more like sugar as regards shape uniformity and size.
The media are distributed typically in five layers. Each layer supports the one above it. Each layer is carefully selected for density, size and shape. AWWA B100 layers are:
- 1/4”x1/8” quartz to cover the filter distributors.
- 1/8”x1/16” quartz to 2.5” depth
- #12/12 high density garnet to 2.5” depth
- #30/40 high density garnet to 2.5” depth
- 45-0.555 mm filter sand (silica) to 24” depth
Our MMF filters are found in a variety of industries including but not limited to:
- Always a good choice for effluent polishing of our DAF and Clarifier systems.
- Parts bath rinse water filtration.
- Turbidity reduction of river and lake water used for process, firefighting, washdown etc.
- Drinking water pre-treatment.
- Sanitary sewer effluent treatment for water re-use and recycling.
- Construction excavating dewatering.
- Well water filtration.
Typical Options Include:
- Mild steel or stainless steel construction
- Special coatings internal and/or external
- XP rated explosion proof or intrinsically safe electrical components
- Air scour assist backwash
- Acid assist backwash
- Different medias including IX Ion Exchange, potassium permanganate and carbon
- Complete control packages
- Pump skids, influent and effluent
- Chemical dosing and FFM Flash-Floc-Mixing Systems for particle size enhancement
- Operator platforms
Need a Quote?
Click here for our Application Questionnaire to obtain a quote.
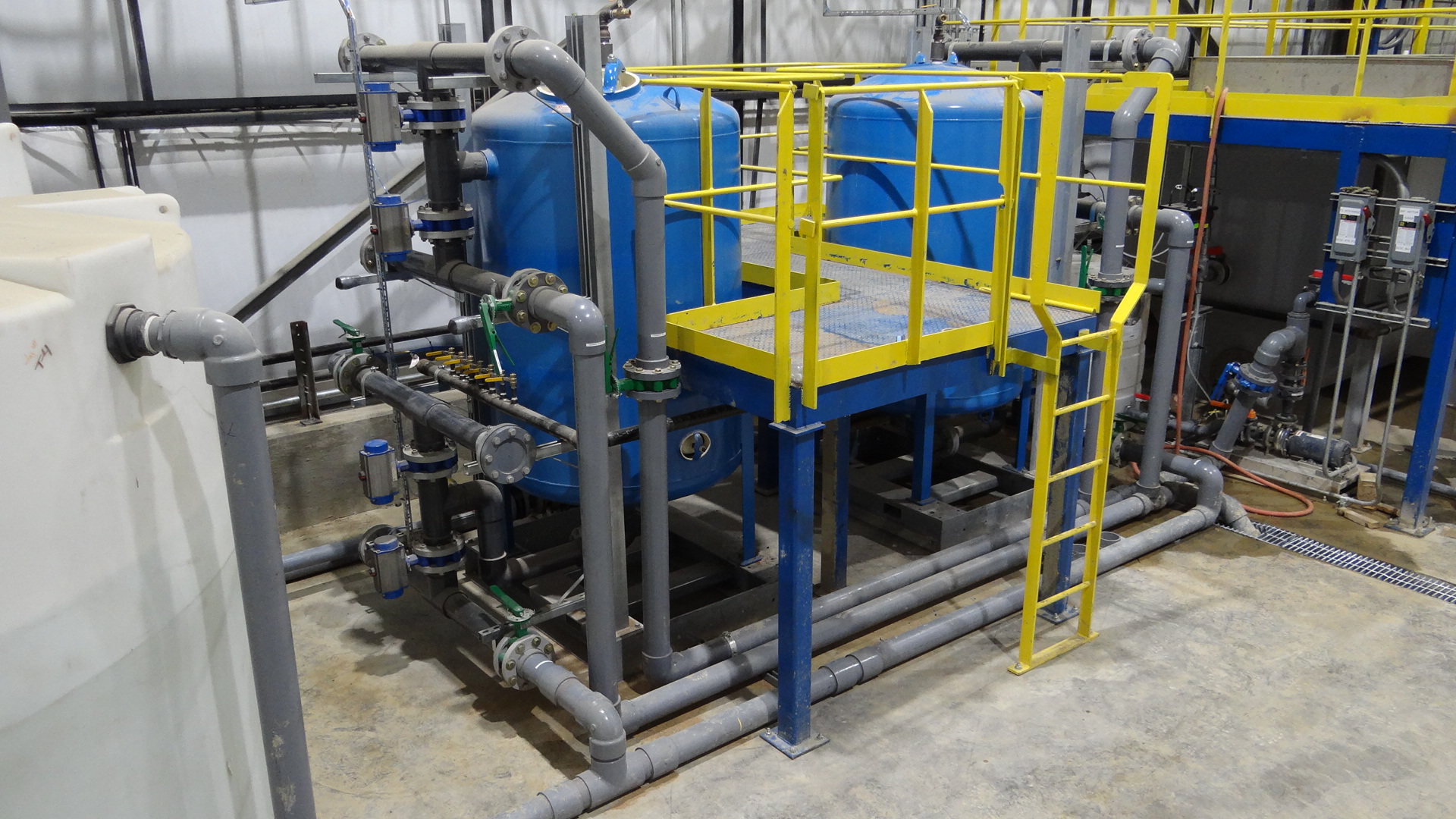
Quality
We use only the highest quality materials, pumps, instruments, valves and controls components to ensure you the heavy duty robust performance you demand in today’s highly competitive market environment. All our systems are built to the highest standards of craftsmanship and are extensively tested throughout the fabrication process. We perform a variety of NDE testing including PQR, UT, XT, full hydro, dye penetrant, ASME pressure testing and of course visual inspections and functional testing both in-shop and in the field.
Controls
We design and build all our own controls in-house to UL-508A Industrial Control Panel standards with strict conformance to NEC, ANSI and NFPA regulations. All panels are built to UL standards and are individually UL certified if required.
Our operator controls interface scheme is the most advanced in the wastewater industry. We offer basic simplified controls to full featured controls systems that use SQL database platforms permitting the generation, archiving and managed all trending and effluent data. Our most advanced controls offer operator input of bench treatability testing that then allow the system .
Tankwash Systems
Our Industrial Tankwash Division designs and builds Railcar and Tank Trailer Internal wash systems to wash everything from Crude oil to Edible oils, from Chemicals to Corn Starch and everything in between. When you wash an industrial tank, you create an industrial wastewater and we take care of that too.
View pdfs for more information: