OWS - Oil Water Separators – ComplianceMaster, API & APC
Applied Mechanical Technology is an industry leader in industrial wastewater treatment components and systems. Since 1997 we’ve been designing and building industrial equipment and systems for variety of industries.
We design and build all our core technology equipment in-house. Our complete line of equipment includes:
- Oil Water Separators,
- DAF Dissolved Air Flotation,
- Inclined plate Clarifiers,
- Multimedia filters
- Controls Packages.
These are the core of our complete systems packages. We complete our systems with strategic OEM relationships for all the other necessary components such as instruments, pumps, valves etc.
As we design and manufacture our core equipment and systems in our own shop we have the flexibility and the ability to configure our systems as needed to meet the most stringent project specifications while exceeding customer’s expectations.

Principal of Operation – Oil Water Separators
Oil Water Separators separate oil particles from water. They have limited capability to remove emulsified oil, either chemical or mechanically emulsified. Simply put, we exploit Stokes Law where a particle of oil or “LNAPL” (Light Non Aqueous Phase Liquid) of a given mass (size and specific gravity S.G.) is calculated to rise at a known rate in a water medium. Generally speaking, the lighter the density, the faster it rises the smaller the Oil Water Separator, conversely the heavier the density the slower it rises the larger the Oil Water Separator. Therefore gasoline (~0.74 S.G.) will separate easier than motor oil (~0.89 S.G.). However, if the oil is denser than water then it will sink and you need a different type of Oil Water Separator. The size of the Oil Water Separator is calculated to ensure that the oil particle is able to rise to the surface before reaching the exit.
The high performance coalescing type Oil Water Separator has the added feature of using coalescing media that equates to surface area and improves performance in a smaller space thereby saving money and getting superior performance. If coalescing media separators were compared to a simple open channel type Oil Water Separator (commonly referred to as an API separator) the open channel separator would be much larger and would not perform as well. Having said that, there is always a place for an API type separator as they are useful if dealing with thick or sticky oils that might otherwise foul coalescing media plates, and they usually have a mechanical surface skimmer to move the thick or viscous scum to the scum chamber. Ordinary Oil Water Separators normally do not have a mechanical surface skimmer but will have an adjustable oil weir that allows the collected floating oil to flow over the weir and into the waste oil chamber. They should also have an influent diffusion baffle to promote laminar flow conditions and a bottom solids/grit chamber. There are some variations to these concepts but certain design criteria are not negotiable to ensure good performance.
The Stokes Law calculation and general Oil Water Separator design guidelines are found in American Petroleum Industry Publication API-421, the bible of the Oil Water Separator industry. Our Compliance Master Oil Water Separators are designed in strict accordance with API 421 with due regard to size, shape, coalescing media surface area, and cross sectional velocity.
All our Oil Water Separators are perfectly suited as front end treatment of oily wastewater prior to additional downstream treatment such as chemical flash/floc, DAF and/or Clarifier. They also are suitable for certain end-of-pipe treatment applications provided no emulsified oil is present.
We make several Models of Oil Water Separators for a variety of applications
1). ComplianceMaster high performance coalescing type Oil Water Separators in eleven standard sizes from 5 to 250 gpm with custom sizes also available. These are designed according to publication API 421 and are extensively used throughout the industry. They employ either slant plate, tilted plate, or honeycomb style coalescing media to put a lot of performance into a relatively small package. The principal of operation is to slow flow, create laminar flow conditions and subject the oil particulate to a coalescing surface where it then impinges on the surface. As more oil impinges, it gathers mass and migrates upward to the oil collection area. Treated water then exits the bottom past the surface sheen baffle. This Oil Water Separator is excellent for removing non-emulsified oils or removing emulsified oils if chemically pre-treatment with acid or demulsifiers. The standard ComplianceMaster models include a waste oil chamber with pump control fittings, and bottom sludge/grit chamber, inlet diffusion baffle, Coalescing media adjustable effluent and oil weirs, and effluent chambers with pump control fittings suitable for pumpout.
2). The ComplianceMaster EcoSep high performance coalescing type Oil Water Separator. This is the economy version of the ComplianceMaster Oil Water Separator. This model has all the same performance features of the ComplianceMaster Oil Water Separator but without a bottom sludge/grit chamber. This Oil Water Separator is suitable for oily wastewater that does not have much suspended solids.
3). The Model APC Applied Pressure Coalescer. This is a super heavy duty high performance coalescing type Oil Water Separator with enhanced features that include;
- Utilizes centrifugal force to enhance oil/solids/water separation by employing a tangential inlet and downward flow path thru a coalescing media.
- Operates under high pressure and high temperature. This feature makes it suitable for a variety of industrial applications where flow is delivered under pressure and prefers to remain under pressure unlike the atmospheric pressure operating conditions of the ComplianceMaster. It is not susceptable to uneven installation conditions and therefore is suitable for shipboard and oil rig platform installations.
- It can be configured with a steep cone bottom instead of the standard shallow dish bottom for superb solids removal. These APC Oil Water Separators are often used in petro chemical plants for treating cooling and other process waters under pressure and as hot as 250F.
API-OWS Oil Water Separator. This is a traditional open channel type Oil Water Separator. The very first kind ever built decades ago. Some refer to it as a wide spot in the pipe. True, it’s typically not a very sophisticated Oil Water Separator but there is more than meets the eye. The Oil Water Separator is sized and designed according to API publication 421 using stokes law. This Oil Water Separator is perfect for removing thick, sticky and highly viscous oil and other floating material that does not flow well and would clog an ordinary coalescing media.
The API-OWS model includes:
- Main separator body with inlet diffusion, open internals, sloped bottom sludge chamber.
- Surface scum skimmer, mechanical multiple flights. Scum beach and scum chamber.
- Adjustable effluent weir
- Effluent chamber with effluent pump and instrument fittings
- Standard options include: Vapor tight cover, bottom auger.
- Optional conversion to DAFloat (see DAF info here) Dissolved Air Flotation
Our Oil Water Separators are found in a variety of industries including – but not limited to:
- Refinery unit and process waters, cooling towers, backwash, produced water.
- Groundwater remediation, hydrocarbon pump & treat.
- Metal stamping. Forming and coating metal parts. Coating preparation using wash and rinse waters, post formed part wash water. Can making operations, conduit and tubing makers, electronics chassis, chemical etching.
- Metal forging operations. Press pit water, fume scrubber water, and NDE test waters.
- Meat preparation. Meat cooking, deli meats, sausage cooking (boiled in water), food prep facility cleaning and sanitizing.
Typical Options Include:
- Mild steel or stainless steel construction.
- XP Explosion proof electrical components.
- Bottom sludge augers
- Complete control packages
- Pump skids, inlet, effluent, oil, sludge.
- Chemical dosing and FFM Flash-Floc-Mixing Systems for emulsion breaking
- Operator platforms.
- Special coatings for highly corrosive application.
- Effluent filters
Need a Quote?
Click here for our Application Questionnaire to obtain a quote.
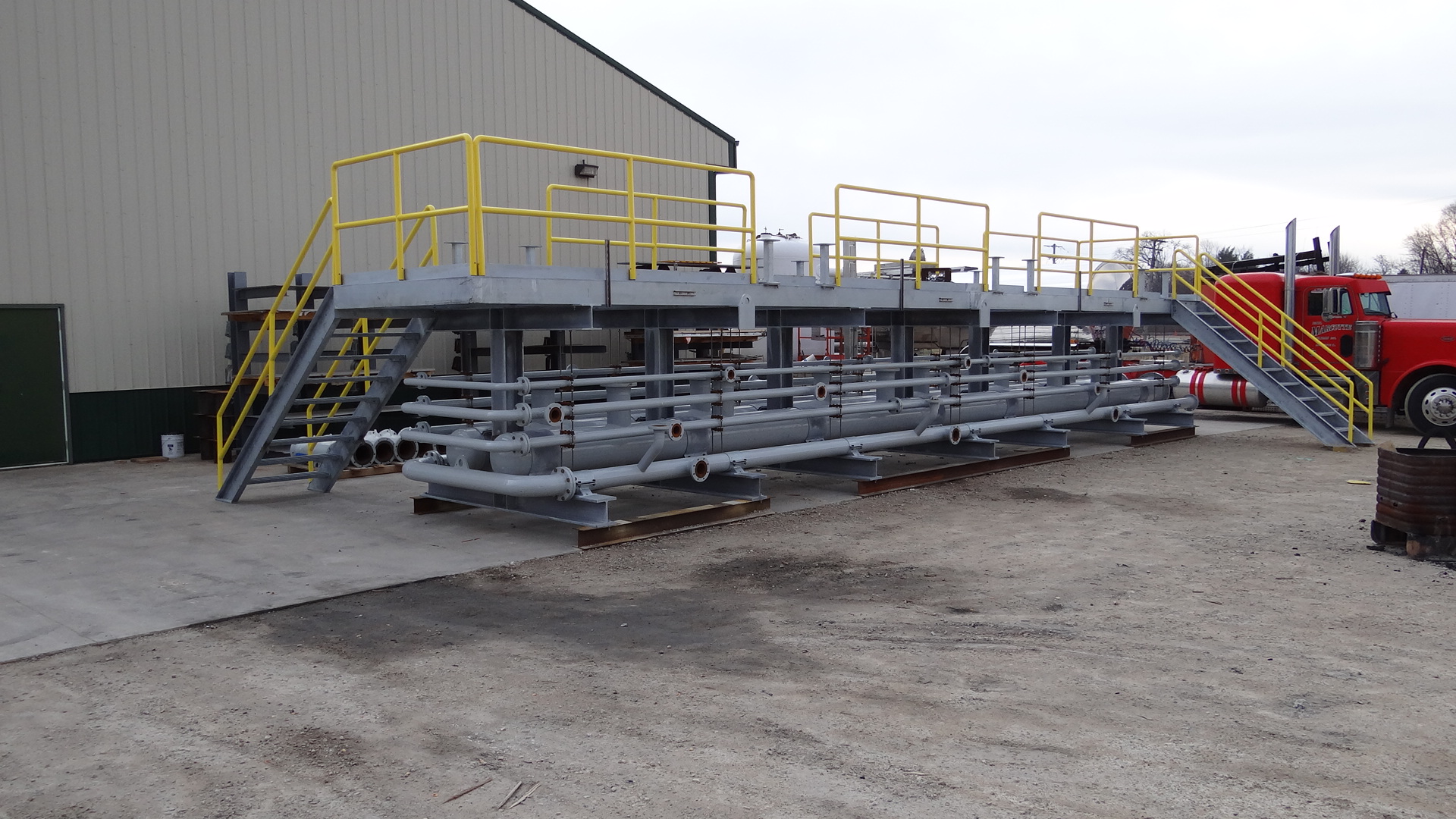
Quality
We use only the highest quality materials, pumps, instruments, valves and controls components to ensure you the heavy duty robust performance you demand in today’s highly competitive market environment. All our systems are built to the highest standards of craftsmanship and are extensively tested throughout the fabrication process. We perform a variety of NDE testing including PQR, UT, XT, full hydro, dye penetrant, ASME pressure testing and of course visual inspections and functional testing both in-shop and in the field.
Controls
We design and build all our own controls in-house to UL-508A Industrial Control Panel standards with strict conformance to NEC ANSI/NFPA 70 regulations. All panels are built to UL standards and are individually UL certified if required.
Our operator controls interface scheme is the most advanced in the wastewater industry. We offer basic simplified controls to full featured controls systems that use SQL database platforms permitting the generation, archiving and managed all trending and effluent data. Our most advanced controls offer operator input of bench treatability testing that then allow the system.
Tankwash Systems
Our Industrial Tankwash Division designs and builds Railcar and Tank Trailer Internal wash systems to wash everything from Crude oil to Edible oils, from Chemicals to Corn Starch and everything in between. When you wash an industrial tank, you create an industrial wastewater and we take care of that too.
View pdfs for more information:
Brochure OWS – APC
Brochure OWS Compliance Master
Brochure OWS Open Channel API